Loss Prevention - Case Study, D/G break-down
- Admin
- Aug 2, 2023
- 3 min read
Updated: Mar 10
D/G break-down & subsequent loss of power
Last month we looked into an intriguing instance involving the simultaneous failure of all D/G’s on a LR1 tanker in Antwerp area. In view of Loss Prevention, this bulletin examines this case study involving the D/G break-down.

Within a short period of time, the ship's three (3) D/Gs all failed in succession, causing power loss off the coast of northern France. It barely made it to the port of Antwerp, where our Client immediately requested that we attend and look into. Oddly enough, all D/Gs had been recently overhauled as part of the ship owner's PMS (scheduled maintenance scheme) when the vessel underwent drydock repairs recently, in May 2023.
Case Assessment
Since all D/G’s had recently been maintained just 2 months prior to the incident, we boarded the vessel with an investigative appetite, to discover what had gone wrong & shed light on this odd incident.
We started by assessing the extent of damages & evaluating the current status/performance of the engines. A maximum of just 30% of their nominal capacity could be achieved. Black smoke was being emitted from the funnel exhaust. The L.O consumption had increased dramatically to 150 ltr/day.
Initial reports from the ship’s engine crew revealed nothing out-of-the-ordinary, prior to the incident. All engine crew members confirmed that the generators had recently been overhauled & maintained, while brand new engine parts were installed.
Discussions with the Ch/Eng were held, where he (hastily enough) blamed the poor quality of spare parts that were installed during the recent drydock. Having not been convinced by the crew reports & being determined to uncover the truth, we decided to become a little more forensic.
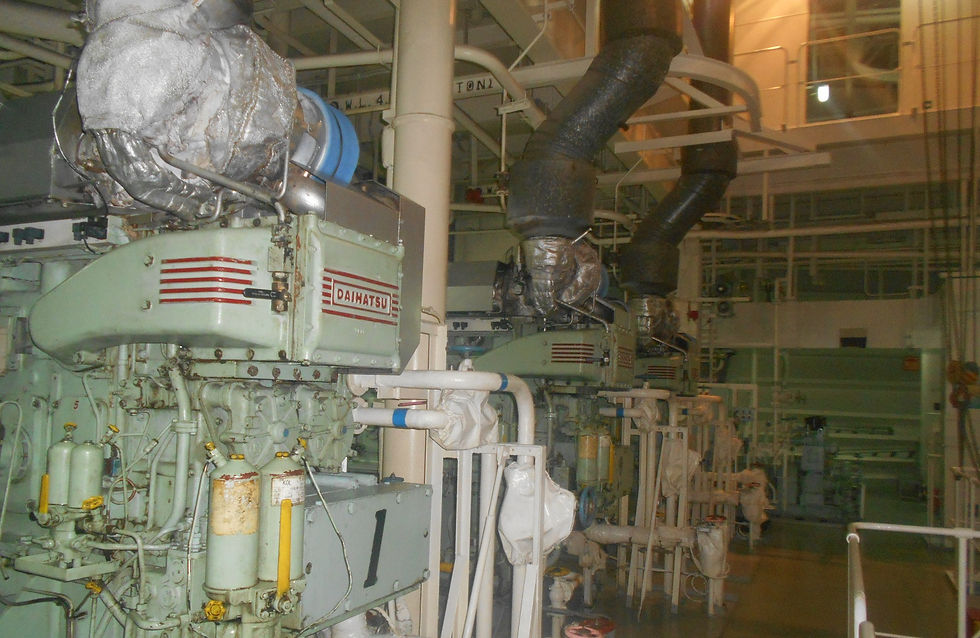
Findings & Analysis / Diagnosis
L.O samples were taken from the generators’ sump tanks & sent for analysis to an accredited laboratory we partner with. Results came back within two (2) days & they were shocking: basic parameters (Viscosity, TAN, Flash Point, etc) wouldn’t match that of a typical D/G L.O, but would correlate more closely to M/E Cylinder Oil (!)
Whilst being bewildered, we presented the evidence to the crew & went for another round of interviews with the crew & looked more closely into the E/R logs. It was finally confessed by one (1) of the less-senior crew members that the D/G L.O ROB qty's were running low whilst at sea & in order to avoid further complications, the Ch/Eng decided to replenish the D/G with M/E Cylinder Oil instead (!), which resulted in this catastrophic chain of events & (almost instant) failure of all three (3) D/G’s.
The ship had to stay at anchorage for repairs for 12 days resulting in hire-loss & huge financial losses for the ship owner.
Lessons Learnt
What are the lessons learnt from this case study, in terms of loss prevention? Who do you think bears the biggest responsibility for this debacle? It would be convenient enough to shift the blame on the Ch/Eng for not being prudent enough to request sufficient quantities of L.O well in advance & for not communicating in a clear & crisp manner to the Head Office the looming danger.
But what if there could be ways to make it easier for the crew onboard to admit mistakes early enough by establishing a ‘no-fault’ culture within the Company’s culture ?
Who do you think bears responsibility for this catastrophic chain of events ?
The Ch/Eng - should have reported the low L.O rob qty's
Company's blame culture
it's more nuanced - comment below
📞 0031 (0) 85 00 45451
Comments