MEG4 Demystified: An Overview of Mooring Equipment Standards
- Admin
- Mar 17
- 11 min read
The maritime industry has made a significant leap in ensuring the safety and efficiency of ship mooring operations with the introduction of the Mooring Equipment Guidelines, Fourth Edition (MEG4). These mooring equipment standards set out recommended minimum requirements for the design, performance, and safety of mooring systems. They address critical aspects such as the use and understanding of mooring lines and tails. MEG4 aims to enhance ship mooring safety by adopting a human-centered design approach and focusing on the design of mooring arrangements.
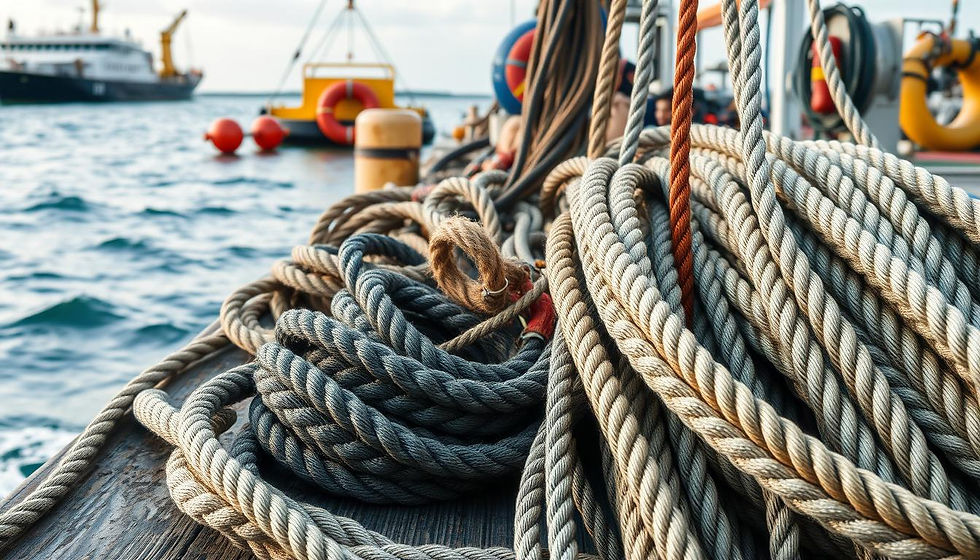
The significance of MEG4 cannot be overstated. Incidents like the Zarga incident at the South Hook LNG terminal in Wales in 2015 highlight the importance of robust mooring equipment guidelines. This article aims to demystify MEG4, equipping ship owners, operators, and crews with the knowledge necessary to ensure meg4 compliance and maintain the highest standards of safety in mooring operations.
The fourth edition of the Mooring Equipment Guidelines (MEG4) was released in July 2018, marking a significant update from the previous edition, which was published in 2005. MEG4 introduces new terminology, such as Ship Design Minimum Breaking Load (SDMBL), Line Design Break Force (LDBF), and Tail Design Break Force (TDBF), which are crucial for understanding the guidelines and ensuring compliance.
Key Takeaways:
MEG4 establishes recommended minimum requirements for the design, performance, and safety of mooring systems.
The guidelines focus on enhancing ship mooring safety through a Human Centered Design approach and increased emphasis on the use and understanding of mooring lines and tails.
Recent incidents highlight the importance of robust mooring equipment guidelines in preventing injuries and fatalities.
MEG4 introduces new terminology, such as SDMBL, LDBF, and TDBF, which are essential for understanding and complying with the guidelines.
The article aims to provide ship owners, operators, and crews with the knowledge necessary to ensure meg4 compliance and maintain the highest standards of safety in mooring operations.
Introduction to MEG4 and Its Importance in Ship Mooring Safety
The Mooring Equipment Guidelines, fourth edition (MEG4), was developed by the Oil Companies International Marine Forum (OCIMF). It marks a significant advancement in ensuring safe and efficient ship mooring practices.
The updated guidelines aim to enhance ship mooring safety & reduce mooring lines snap-back accidents. They provide comprehensive guidance on various aspects, including the purchase, condition monitoring, and retirement of mooring lines and tails. MEG4 introduces new chapters on human factors, jetty design, ship shore interface, and alternative technologies. These are crucial for mooring operations.
One of the key aspects addressed in MEG4 is the introduction of new terminology. This clarifies confusion previously seen in the industry regarding line strength and mooring procedures. Terms such as Ship Design Minimum Breaking Load (SDMBL), Line Design Break Force (LDBF), and Working Load Limit (WLL) have been defined. They standardize practices and ensure consistency across the industry.
The current configuration allows for mooring lines to meet 100-105% of the SDMBL as validated by independent class societies as per MEG4 requirements.
Regular winch brake render testing should start at 60% of the mooring line LDBF to enhance safety during mooring operations. The transition from older MEG3 ropes to MEG4 ropes is underway. This allows for an acceptable Line Management Plan (LMP) after two years of implementation.
Mooring Line Material | LDBF | WLL |
Steel Wire Ropes | 100-105% of SDMBL | 55% of SDMBL |
Synthetic Cordage (except Nylon) | 100-105% of SDMBL | 50% of SDMBL |
Nylon (tested wet and spliced) | 100-105% of SDMBL | 50% of SDMBL |
Key Changes and Updates in MEG4 Compared to Previous Versions
MEG4 marks a significant leap in mooring safety. It offers detailed guidance on safe mooring procedures, mooring line management, and mooring equipment testing. The goal is to lower mooring line failure incidents, which have led to many fatalities and increased accident rates.
Enhanced Guidance on Purchasing, Condition Monitoring, and Retirement of Mooring Lines and Tails
MEG4 provides updated rules for purchasing, monitoring, and retiring mooring lines and tails. It advises that the Line Design Break Force (LDBF) for ropes should be 100-105% of the Ship Design Minimum Breaking Load (SDMBL). For tails, the Tail Design Break Force (TDBF) should be 125-130% of the SDMBL. Mooring lines must retain an average residual strength of at least 75% of the SDMBL before they can be retired.
Mooring Component | Design Break Force |
Ropes (LDBF) | 100-105% of SDMBL |
Tails (TDBF) | 125-130% of SDMBL |
New Chapters on Human Factors, Jetty Design, Ship Shore Interface, and Alternative Technologies
MEG4 introduces new chapters focusing on vital mooring safety aspects:
Human Factors in Mooring Design
Jetty Design and Fittings
Ship Shore Interface
Alternative Technologies
Understanding the New Terminology Introduced in MEG4
MEG4 introduces new terminology to enhance the safety of ship and terminal personnel within mooring operations. These terms standardize equipment management and provide a clear framework for mooring equipment selection and maintenance.
Ship Design Minimum Breaking Load (SDMBL)
The Ship Design Minimum Breaking Load (SDMBL) is a critical parameter against which all components of a ship's mooring system are sized and designed with defined tolerances. According to MEG4, the line design break force (LDBF) of the mooring line shall be within 100%-105% of the SDMBL, ensuring adequate strength and safety during ship mooring operations.
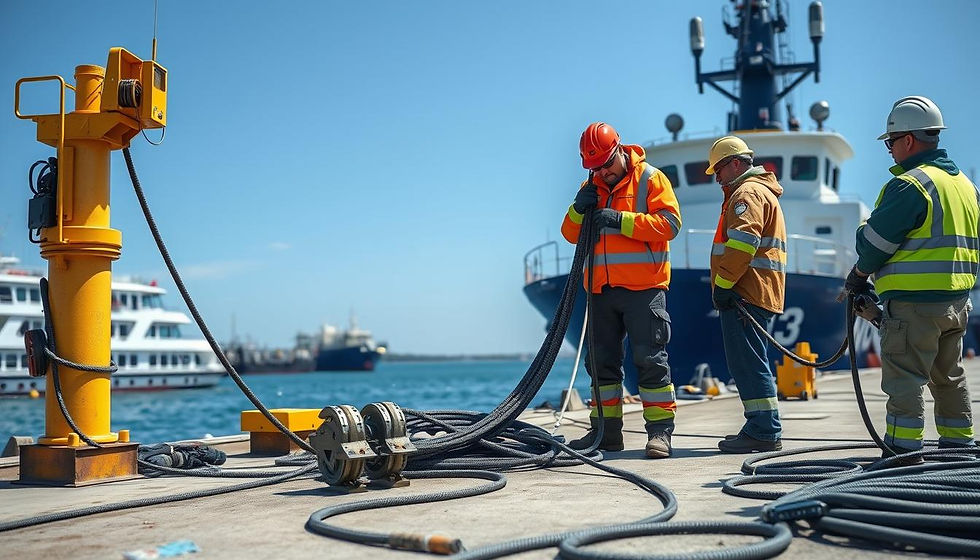
Line Design Break Force (LDBF) and Tail Design Break Force (TDBF)
MEG4 defines the Line Design Break Force (LDBF) and Tail Design Break Force (TDBF) as the minimum forces at which new, dry, spliced mooring lines and tails will break, respectively. The TDBF shall be between 125%-130% of the SDMBL, providing an additional safety margin. Ships built according to MEG3 or earlier may use lines/tails with strength specifications for un-spliced rope according to ISO 2307 testing.
Parameter | Value |
LDBF | 100%-105% of SDMBL |
TDBF | 125%-130% of SDMBL |
Working Load Limit (WLL) for Steel Wire Ropes and Cordage
The Working Load Limit (WLL) is the maximum load a mooring line should be subjected to in operational service, expressed as a percentage of SDMBL. Regular mooring equipment inspection and adherence to the WLL ensure the longevity and safety of the mooring system.
The Mooring System Management Plan (MSMP) and Line Management Plan (LMP) are essential tools for documenting and managing the maintenance, inspection, and retirement of mooring lines throughout their operational life cycle, in compliance with meg4 certification requirements.
Importance of Line Management Plan (LMP) and Mooring System Management Plan (MSMP)
The Line Management Plan (LMP) and Mooring System Management Plan (MSMP) are vital for ship mooring guidelines and mooring line safety under MEG4 standards. These plans act as dynamic documents, ensuring the effective meg4 implementation and adherence to mooring equipment requirements throughout a vessel's life cycle.
The LMP (Line Management Plan) is customized for each operator, ship type, and trade route. It outlines the maintenance, inspection, and retirement criteria for mooring lines. It includes crucial records like mooring hours, line inspection plans, and retirement criteria from manufacturers and operators. The LMP can stand alone or be part of existing safety or maintenance systems, needing regular updates and easy access for compliance checks and training.
The MSMP (Mooring System Management Plan) complements the LMP, enhancing a ship's safety management system. It uses a goal-based approach, defining key elements with high-level goals and detailed functional requirements. It has seven parts, covering:
general ship particulars,
mooring equipment design philosophy,
detailed equipment lists,
inspection and maintenance strategies,
risk and change management,
records and documentation, and
the Mooring System Management Plan Register (MSMPR)
New Standards for Purchasing Mooring Lines According to MEG4
The fourth edition of OCIMF Mooring Equipment Guidelines (MEG4), released in July 2023, sets new standards for mooring line purchases to boost ship mooring safety. This update is the result of a collaborative effort by a diverse group. It includes members from shipping trade organizations, mooring line manufacturers, shipyards, and OCIMF members. The meg4 standards reflect lessons from past incidents, focusing on failures of HMSF mooring lines.

Choosing the right mooring line involves several key considerations, as outlined in the meg4 safety measures. These include load-bearing linear tenacity, vessel type, and the frequency and type of mooring. Other factors include line tenacity, axial compression resistance, and temperature conditions. The specifications of the vessel's mooring equipment for ships are also crucial.
Factors to Consider When Selecting the Right Mooring Line
Load-bearing linear tenacity
Vessel type and specifications
Frequency and type of mooring operations
Line tenacity and axial compression resistance
Temperature conditions
Compatibility with the vessel's mooring equipment
Required Specifications and Documentation
To meet MEG4 standards, certain specifications and documentation are essential for purchasing mooring lines. These include:
Material composition (without mentioning brand names)
Reason for replacing the mooring line
Working Load Limit (WLL) defined as:
55% of the SDMBL for steel wire ropes
50% of the SDMBL for synthetic cordage
Compliance with the Line Management Plan (LMP) specific to each operator, ship type, mooring line type, and trade route
Implementing a Three-Step Approach to MEG4 Compliance
Compliance with MEG4 demands a structured method. Ship owners and operators can comply by adopting a three-step strategy, as per below:
Planning: Optimal Mooring Line Selection and LMP Development
The initial step towards MEG4 compliance is meticulous planning. It entails choosing the right mooring lines based on the Ship Design Minimum Breaking Load (MBL). This is a key factor as per OCIMF standards. The Line Design Break Force (LDBF) must be 100-105% of the Ship Design MBL for all materials except nylon, which requires wet testing. Tail Design Break Force (TDBF) is set at 125-130% of the Ship Design MBL to account for wear on tails.

Creating a detailed Line Management Plan (LMP) is vital in the planning phase. The LMP must document mooring hours, line inspection records, and manufacturer guidelines. Working closely with rope manufacturers during this phase ensures the selection and development of the LMP align with MEG4 standards.
Training: Crew and Executive Education on MEG4 Standards
The second step emphasizes education and training. Crew members and shore staff need to understand the latest standards for safe operations. Certain rope manufacturers may also offer training on safety, maintenance, inspection, and management of mooring lines, adhering to OCIMF MEG4, IMO, and ISO/CI standards.
Training should cover critical MEG4 aspects, such as maximum operational Working Load Limits (WLL) for steel wire ropes (55% of Ship Design MBL) and synthetic cords (50% of Ship Design MBL). It's crucial to understand the need for maintaining a minimum residual strength of 75% of the original design MBL before line retirement. Comprehensive training helps in cultivating a safety and compliance-focused culture.
Monitoring and Inspection of Mooring Lines under MEG4
To meet MEG4 standards, vessels must have a Mooring System Management Plan (MSMP) and Line Management Plan (LMP). The MSMP outlines the design philosophy, equipment list, inspection, maintenance, and retirement strategies. The LMP includes records of mooring hours, line inspections, retirement criteria, test reports, and manufacturer's guidance. Compliance with these plans may involve review and inspection by vetting auditors.
Environmental Criteria to Consider
Mooring lines can deteriorate due to aging. Several environmental factors are the cause for this. These include wind and current direction and force, temperature, sea swell, and humidity. Exposure to moisture, UV light, chemicals, and extreme temperatures can deteriorate mooring lines. Regular inspections are essential for maintaining safety and operational integrity.
Other Factors Affecting Mooring Line Performance
Environmental factors are not the only considerations. The type of work, hours of operation, and mooring operation and equipment also impact performance. Protection of mooring lines and their construction and specification are also critical. Replacement mooring lines must match the original specifications for safety and operational integrity. A MEG4 compliant certificate may be required for replacement lines in certain trades.

The Role of Technology in Monitoring and Inspection
Technology is essential in monitoring and inspecting mooring lines. It is very important to perform regular on-board visual quality inspections & compile comprehensive reports There exist specific mooring line inspection software to aid these inspections. These tools help ship owners and operators maintain a meg4 compliance checklist and ensure the safety of their mooring equipment.
A typical inspection routine may comprise the following:
Inspection Type | Frequency | Key Points |
Routine Visual Inspection | Daily | Check for visible damage, wear, or deterioration |
Detailed Line Inspection | Monthly | Examine the entire length of the line for internal and external defects |
Manufacturer's Inspection | Annually | Comprehensive inspection by the line manufacturer or a certified third-party inspector |
Benefits of Adopting MEG4 Standards for Ship Owners and Operators
One of the major benefits of implementing MEG4 standards is reduction of operational costs. By following the guidelines for purchasing, monitoring, and retiring mooring lines, ship owners can extend their equipment's life. This leads to cost savings over time.
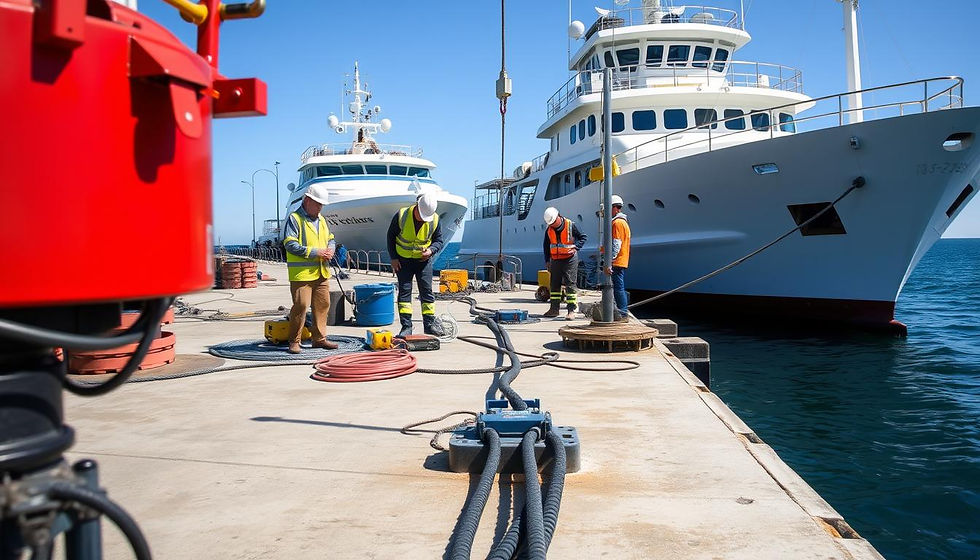
Adopting MEG4 standards also enhances safety for crew members and shore workers. The guidelines stress the importance of regular crew training and competency assessments. This ensures that all personnel involved in mooring operations are well-versed in safety procedures.
Conclusion
MEG4, the latest Mooring Equipment Guidelines edition, offers a comprehensive approach to mooring safety by incorporating industry updates and advancements. It provides a framework for designing, selecting, operating, and maintaining mooring systems.
The guidelines introduce terms like Line Design Break Force (LDBF) and Working Load Limit (WLL) to clarify mooring line properties, preventing misunderstandings that could lead to accidents.
Implementing MEG4 involves a three-step approach, including a Line Management Plan (LMP) and a Mooring System Management Plan (MSMP), ensuring correct selection, maintenance, and retirement of mooring equipment, considering environmental and operational demands.
Regular inspections and mooring line rotation are essential to prevent failures and snap-back incidents, which pose risks to personnel and equipment.
Adopting MEG4 standards minimizes risks and costs, prioritizing crew well-being and emphasizing human-centered design in mooring operations.
As the maritime industry evolves, following MEG4 guidelines is crucial for a safer and more efficient future in ship mooring.

FAQ
What is MEG4?
MEG4 is the latest update to the Mooring Equipment Guidelines. It sets out minimum requirements to enhance mooring system design, performance, and safety. It offers detailed guidance on purchasing, monitoring, and retiring mooring lines and tails. New chapters cover human factors, jetty design, ship-shore interface, and alternative technologies.
How does MEG4 differ from previous versions?
MEG4 brings new insights on purchasing, monitoring, and retiring mooring lines and tails. It also improves documentation of mooring equipment. The update includes chapters on Human Factors in Mooring Design, Jetty Design and Fittings, Ship Shore Interface, and Alternative Technologies.
What new terminology is introduced in MEG4?
MEG4 introduces key terms like Ship Design Minimum Breaking Load (SDMBL) and Line Design Break Force (LDBF). It also defines Tail Design Break Force (TDBF) and Working Load Limit (WLL) for steel wire ropes and cordage. These terms are crucial for designing and sizing a ship's mooring system.
What is the importance of the Line Management Plan (LMP) and Mooring System Management Plan (MSMP)?
The Line Management Plan (LMP) manages the operation and retirement of mooring lines and tails. It outlines the requirements, assumptions, and evaluation methods for line retirement. The Mooring System Management Plan (MSMP) complements the ship's Safety Management System (SMS). It identifies key elements of the mooring system, sets high-level goals, and provides detailed functional requirements.
How can ship owners and operators implement MEG4 compliance?
Implementing MEG4 compliance involves a three-step approach. The first step is planning, which includes selecting optimal mooring lines and developing LMPs according to MEG4. The second step is training, which involves courses from rope experts. These courses educate crew and executives on safety, maintenance, inspection, and management of mooring lines.
What factors should be considered when monitoring and inspecting mooring lines under MEG4?
When monitoring and inspecting mooring lines, consider environmental factors like wind, current, temperature, sea swell, and humidity. Other factors include the type of work, hours of operation, mooring operation type, and equipment protection. The construction and specification of the mooring line or tail also play a role.
What are the benefits of adopting MEG4 standards for ship owners and operators?
Adopting MEG4 standards offers several benefits. It reduces operational costs by extending mooring line life and minimizes risks during mooring operations. It also enhances safety by entrusting line monitoring to experts. Compliance ensures that mooring systems are designed, maintained, and operated to the highest safety standards.
Comments