What are the different types of ship drydocks?
- Admin
- Aug 14, 2024
- 10 min read
Updated: Jan 22
Merchant vessels must undergo a complete hull survey in a dry dock twice within a 5-year period, as per IACS requirements. This underlines the pivotal role of ship drydocks in maintaining vessel safety and seaworthiness. These facilities are vital for the marine engineering and shipbuilding sectors, offering a dedicated dry space for vessel repair, maintenance, and construction. Different types of drydocks serve various ship sizes and needs, each with distinct benefits and constraints.

For seagoing vessels, the primary drydock types include graving drydocks & floating drydocks, while marine railways are used for smaller ships. Vertical lift drydocks are used for small boats.
Graving drydocks, which -in essence- are carved out basins, handle larger vessels and support retrofits and modifications. In contrast, floating drydocks are designed for portability and space efficiency, making them perfect for accommodating damaged ships.
Marine railways are tailored for vessels up to 10,000 tonnes. Meanwhile, vertical lift drydocks and alternative solutions like lifts, cranes, and air bags are suited for smaller boats and yachts.
Key Takeaways
Drydocks are essential for ensuring vessel safety and seaworthiness
Various types of drydocks cater to different ship sizes and requirements
Graving drydocks are ideal for larger vessels and support retrofits and modifications
Floating drydocks are portable and space-efficient, ideal for accommodating damaged ships
Marine railways, vertical lift drydocks, and alternative methods cater to smaller vessels and yachts
Introduction to Ship Drydocks
Drydocks play a vital role in the maritime industry, essential for building, repairing, and maintaining ships. These specialized facilities allow vessels to be positioned on dry land, facilitating comprehensive inspections, repairs, and modifications to parts that are usually underwater. The dry docking process is crucial for ensuring the safety, reliability, and durability of ships. Drydocks are indispensable assets in the maritime sector.
Definition and purpose of drydocks
A drydock is a basin that can be flooded to float a load (in our case, a ship), then drained for the load (i.e the ship) to rest on a dry platform. They are used for constructing, maintaining, and repairing ships, boats, and other watercraft. The main purpose of a drydock is to expose a vessel's underwater parts for inspection, cleaning, painting, and repairs. This process is vital for maintaining ships' structural integrity, performance, and safety throughout their life.
Importance of drydocks in the maritime industry
Drydocks are vital to the maritime industry, enabling efficient ship repair and maintenance. Regular dry docking is essential for ships to meet international safety standards and remain seaworthy. Drydocks also support vessel construction by providing a controlled environment for assembling and launching new ships.
The availability of suitable drydocks affects the maritime industry's growth and competitiveness, impacting the efficiency and cost-effectiveness of ship maintenance and repair.
Dry Docking Aspect | Significance |
Frequency | Vessels typically undergo dry-docking once every five years for a special survey, with midway surveys also possible for inspections (called 'intermediate surveys') and maintenance. |
Draining Time | The draining of seawater from the dock during dry-docking can take about 4-8 hours, depending on the vessel's size. |
Ship's Hull Treatment | Hull treatment during dry-docking can improve a ship's energy efficiency and reduce daily fuel consumption. |
Anti-fouling Paint | Advanced anti-fouling paint is applied to vessels during dry-docking to minimize deterioration rates. |
The maritime industry heavily relies on drydocks for ship safety, efficiency, and reliability. By offering a controlled environment for maintenance, repair, and construction, drydocks significantly contribute to the global shipping network's smooth operation. They are key to the maritime sector's growth.
Graving Drydocks
Graving drydocks, also known as basin drydocks, are vital in the maritime industry. They provide a secure, efficient space for ship construction, repair, and maintenance. These structures are built into the ground and can be filled with water for vessel entry and exit. They are equipped with a dock gate, which can be moved, to accommodate for ship's entry/exit.

Construction and design of graving drydocks
Modern graving drydocks use reinforced concrete, with strong walls and steel gates to keep water out. Their rectangular shape makes the most of space and fits a variety of vessel sizes. Building them involves digging the area, laying a concrete base, and putting up walls and gates. Systems for pumping water control the dock's water level during vessel docking and undocking. The size of graving drydocks depends on their purpose and the vessels they serve.
For instance, China's Dalian COSCO shipyard has the longest dry dock at 700 meters. It can handle over 200 ships a year of different types.
Advantages and disadvantages of graving drydocks
Graving drydocks have several benefits over other types. They are on land, making it easy to bring in supplies and services. They're efficient for big repairs, upgrades, and changes. They can also handle bigger vessels than floating drydocks or marine railways, saving costs for similar-sized ships. But, graving drydocks have their downsides. Getting vessels in and out takes time because the dock must be filled and emptied. As they get older, they cost more to maintain. Regular upkeep is needed to keep the concrete strong and the gates and pumps working right.
Advantages | Disadvantages |
Land-based location for easy access to supplies and services | Time-consuming docking and undocking process |
Accommodates larger vessels compared to other drydock types | Increased maintenance costs as the dock ages |
Cost-effective for docking ships of similar sizes | Requires regular upkeep of concrete structure, gates, and pumping systems |
Despite the challenges, graving drydocks are key for shipyards globally. They help handle a broad range of vessels efficiently, ensuring top standards in ship building, fixing, and upkeep.
Floating Drydocks
Floating drydocks are essential for ship maintenance and repair, especially in remote areas or during salvage operations. They are a cost-effective and portable option for a broad range of ships, from small to mid-sized vessels.
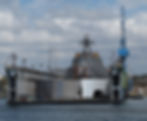
The process of operating a floating dock involves partially submerging it, allowing a ship to be placed inside. After positioning the vessel, the dock's ballast tanks are drained. This action causes the dock to rise, while supporting the ship on blocks. This setup allows for repairs on the hull, propellers, and underwater parts.
Advantages of Floating Drydocks
Floating drydocks have several advantages over traditional graving docks:
Cost-effective maintenance and repair
Ability to service ships in remote locations
Portability, allowing the dock to be moved as needed
Adaptability to accommodate a variety of vessel sizes
These benefits make floating drydocks a preferred choice for many shipyards and maritime businesses. They offer a flexible and efficient way to maintain and repair vessels. Various types of dry docks, including floating docks, are crucial for ensuring ships remain seaworthy and safe.
Limitations of Floating Drydocks
Despite their advantages, floating drydocks have limitations:
Vulnerability to tides and windy weather conditions
Limited access points for equipment and personnel, which can slow down operations
Potential instability during extreme weather events
To overcome these limitations, careful planning and monitoring of weather conditions are crucial when using floating drydocks. Proper training of personnel and implementing safety measures can also ensure smooth operations of these maritime assets.
Floating drydocks are indispensable tools for maintaining and repairing ships, particularly in remote locations or during vessel salvage operations.
Marine Railways
Marine railways, also called slipways, are a distinct form of drydock, employing an inclined track system to lift vessels out of the water for upkeep, repairs, or building. This approach provides a cost-effective and efficient method for shipyards and vessel proprietors, especially for smaller to medium-sized ships.
Functionality of marine railway drydocks
The operation of a marine railway drydock hinges on its inclined track, which stretches from the shore into the water. The vessel is placed onto a cradle or carrier that glides along the track, facilitating a seamless shift from the water to the drydock. A robust hauling machine, equipped with gears and cables, pulls the cradle and vessel up the inclined track, effectively removing the ship from the water.

Suitability for different types of vessels
Marine railways are particularly well-suited for vessels weighing up to 10,000 tonnes. They are an ideal choice for smaller to medium-sized ships, such as:
Fishing boats
Tugboats
Barges
Coastal cargo ships
Offshore support vessels
The versatility of marine railways allows them to accommodate a broad range of vessel types and sizes, making them a flexible solution for shipyards serving diverse clientele.
Drydock Type | Vessel Weight Capacity | Inclined Track | Hauling Machine |
Marine Railway | Up to 10,000 tonnes | Yes | Geared hauling system |
Graving Dock | Varies, can accommodate large vessels | No | Not applicable |
Floating Drydock | Varies, can accommodate large vessels | No | Not applicable |
Marine railways present a unique and efficient solution for drydocking small to medium-sized vessels. Their inclined track design, cradle support system, and powerful hauling machines render them an economical and convenient option for shipyards and vessel owners alike.
Vertical Lift Drydocks
Vertical lift drydocks are a distinct drydocking system featuring a lift platform supported by hoists or jacks on each side. This design enables vessels to be efficiently lifted and lowered. It's ideal for shipyards with deep-water berths. The hoists or jacks, situated on pier structures, move in sync to keep the platform level during lifting.
Vertical lift drydocks stand out for their cost-effectiveness, especially when an existing deep-water berth is present. They require minimal dredging and fill, making installation efficient and economical.
Advantages | Disadvantages |
Cost-effective for existing deep-water berths | Unable to accommodate vessels with trim |
Minimal dredging and fill requirements | Requires precise synchronization of hoists or jacks |
Efficient lifting and lowering of vessels | Higher lift capacity needed compared to vessel weight |
Yet, vertical lift drydocks have their limitations. They cannot handle vessels of medium or large size, limiting their lifting capabilities to smaller boats. Moreover, the synchronization of the hoists or jacks is essential for stability during lifting.
Vertical lift drydocks are an innovative solution for shipyards aiming to enhance drydocking capabilities while reducing dredging and fill operations.

Despite the challenges, these drydocks are widely chosen for their efficiency and cost-effectiveness, but they are limited to smaller boats.
Factors Influencing Drydock Selection
Choosing the right drydock for a vessel involves several critical factors. These include the vessel's size, condition, and repair needs. The vessel's schedule and budget also significantly impact the decision. Ensuring optimal results requires a thorough evaluation of these factors.
Size and Condition of the Vessel
The vessel's size is a primary factor in dry dock selection. Different drydocks cater to varying vessel sizes. For instance, large vessels like supertankers need graving drydocks, which are excavated basins that can be flooded and drained. Smaller vessels, such as tugboats, are better suited for floating drydocks or marine railways.
The vessel's condition is also crucial. Ships needing extensive repairs benefit from graving drydocks' stability and support. Floating drydocks are ideal for vessels that cannot easily enter a graving dock due to their condition or location.
Nature of Repairs and Maintenance Required
The type and extent of repairs or maintenance needed affect drydock selection. Graving drydocks excel in handling major repairs, engine overhauls, and extensive retrofitting. They offer a stable environment and ample space for heavy machinery. Floating drydocks are better for routine maintenance like hull cleaning, painting, and minor repairs. They provide a convenient and cost-effective solution for vessels needing quick turnaround times with minimal disruption.
The global floating dry dock market is expected to grow at an annual rate of 5.8% from 2021 to 2026, with Asia Pacific expected to have the highest demand due to increasing maritime activities in the region.
Vessel Schedule and Budget Considerations
The vessel's schedule is crucial in drydock selection, impacting shipping operations and revenue. The drydock's proximity to the vessel and available repair slots must be considered to minimize downtime and ensure timely completion.
Drydock Type | Suitable Vessel Size | Repair Capabilities | Cost Considerations |
Graving Drydock | Large vessels (e.g., supertankers, container ships) | Major structural repairs, engine overhauls, retrofitting | Higher initial investment, longer repair times |
Floating Drydock | Small to medium-sized vessels | Routine maintenance, minor repairs | Cost-effective, quicker turnaround times |
Marine Railway | Small vessels (e.g., tugboats, fishing boats) | Routine maintenance, minor repairs | Economical, suitable for vessels with quick repair needs |
Choosing the right drydock is a complex decision that requires careful consideration of multiple factors. By evaluating the vessel's size, condition, repair requirements, schedule, and budget, ship owners can select the most appropriate facility to ensure efficient and cost-effective maintenance and repairs.
Conclusion
Dry docks are pivotal in the maritime world, crucial for the building, upkeep, and fixing of ships. Their significance is immense, ensuring ships are safe, long-lasting, and perform well. With options like graving, floating, marine railways, and vertical lifts, ship owners can pick the best fit for their needs. These choices depend on the ship's size, repair needs, schedule, and budget. Advances in technology are making dry-docking more efficient and precise. The use of computer-aided design, automation, robotics, sensors, and data analytics is transforming dry docks. This integration is enhancing maintenance and boosting safety at sea. A deep understanding of dry dock types and their uses is key to smart dry dock choices.
In summary, dry docks are essential for keeping ships in prime condition and meeting safety standards. By embracing technology and considering the right factors for dry dock selection, ship owners can refine their maintenance plans. This approach benefits the maritime sector's safety and efficiency.
FAQ
What is a dry dock, and why is it important in the maritime industry?
A dry dock is a specialized area for the construction, repair, and upkeep of ships and boats. It's vital for the maritime sector. Here, vessels undergo inspections, repairs, and maintenance crucial for their safety and longevity.
What are the main types of dry docks used for seagoing vessels?
For seafaring vessels, the primary dry dock types are graving and floating dry docks. Other forms include marine railway, vertical lift dry docks, and alternative methods like lifts, cranes, and air bags.
How do graving dry docks work, and what are their advantages?
Graving dry docks are essentially pits filled with water that are drained to expose the ship's hull. Constructed from solid concrete, they can handle larger ships. Their land-based setup facilitates easy access to tools and services, making them ideal for retrofitting and modifications.
What are floating dry docks, and how are they different from graving dry docks?
Unlike graving dry docks, floating dry docks are U-shaped structures designed for salvage operations. They submerge to allow damaged ships to slide inside. Once inside, they are deballasted, supporting the vessel on blocks. These docks are cost-effective, portable, and can be situated near or away from shore.
How do marine railway dry docks function, and what vessels are they suitable for?
Marine railway dry docks use tracks extending into the water, similar to railways. Ships are moved on a cradle along these tracks for easy launching and maintenance. Suitable for vessels up to 10,000 tonnes, they offer an economical and convenient solution for owners.
What factors should be considered when choosing a dry dock for a vessel?
Choosing the right dry dock involves evaluating several factors. Consider the vessel's size, repair needs, schedule, and proximity to dry docks. Also, think about the urgency of repairs and the budget.
How is technology improving the operational efficiency of dry docks?
Technology is transforming dry docks. Computer-Aided Design (CAD) optimizes shipbuilding, while automation and robotics streamline docking activities. Internet of Things (IoT) sensors and predictive analytics monitor ship health in real-time, spotting potential issues early.
What are the key considerations for marine surveyors when conducting surveys on vessels in dry docks?
Marine surveyors must assess the vessel's type and size, the survey's purpose, and relevant regulations. They ensure the dry dock meets the vessel's needs and safety standards are followed during the survey.
What role does a technical superintendent play in the dry-docking process?
A technical superintendent oversees the dry-docking process, ensuring repairs and inspections are done as planned within budget and time. They coordinate with the ship owner, shipyard, and stakeholders, solving any issues that arise during the dry-docking period.